Granite quarries extract large, solid pieces of natural stone known as granite blocks. Granite, an igneous rock formed from the cooling and solidification of magma deep within the Earth’s crust, possesses durability, strength, and unique aesthetic qualities. These attributes make granite blocks highly prized for various construction, landscaping, and design applications.
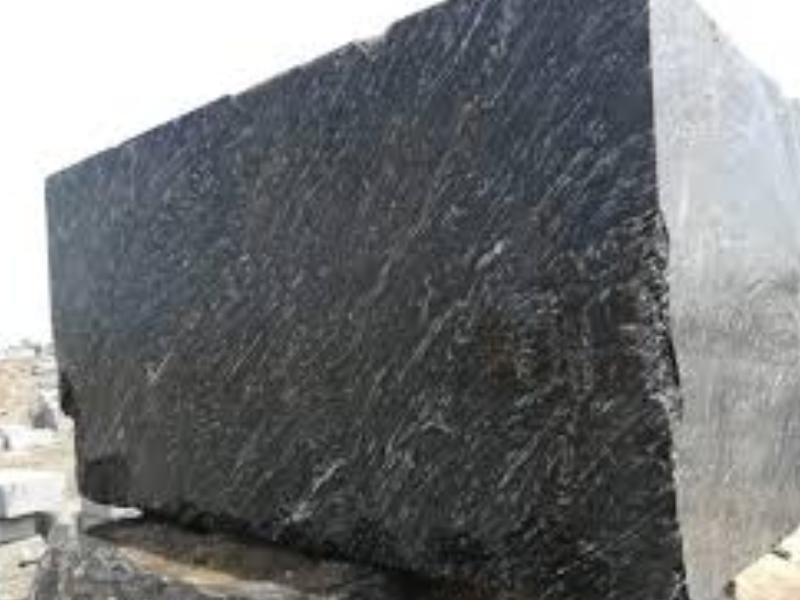
The natural beauty of granite blocks, featuring a range of colours, patterns, and textures resulting from the minerals present in the rock, has earned them renown. Common colours of granite include shades of white, grey, black, pink, and red, with variations in veining and speckling adding to the stone’s visual appeal.
When granite blocks are first extracted from quarries, they are typically rough and irregular in shape. These blocks can vary in size, ranging from relatively small to massive pieces weighing several tons. Once extracted, granite blocks undergo further processing to transform them into usable products such as slabs, tiles, monuments, or dimensional stone for architectural and decorative purposes.
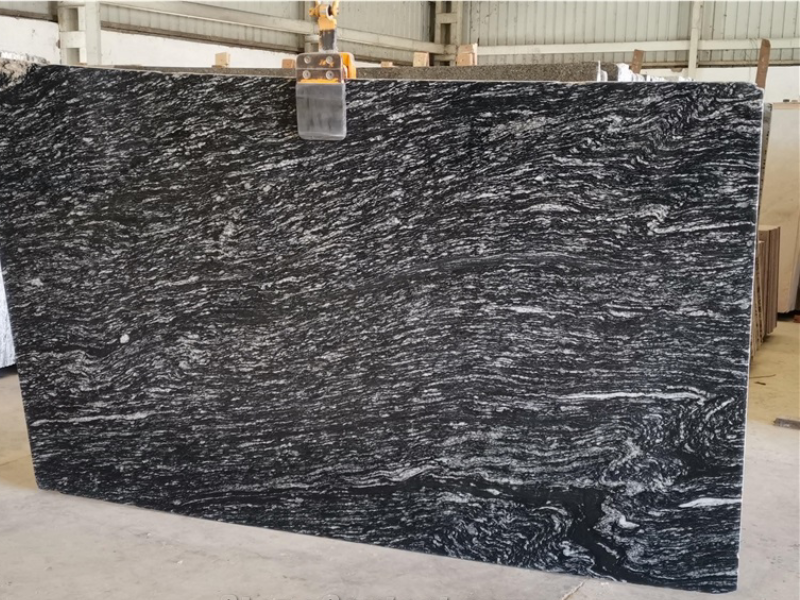
How Are Granite Blocks Sourced From Quarries?
Granite blocks are sourced from quarries through a process known as quarrying or extraction. This process involves several stages, each aimed at safely and efficiently retrieving the granite blocks from their natural geological formations.
Given our commitment to sustainability and safety, we exclusively source granite through non-explosive methods. Therefore, we will focus solely on discussing granite quarrying and processing using non-explosive methods.
Quarry sites are carefully chosen based on the presence of granite deposits and other geological factors. Geologists and surveyors assess the quality and quantity of granite reserves to determine the viability of the quarry site.
Heavy machinery, such as bulldozers and excavators, is utilized to clear the quarry site of vegetation, topsoil, and any other surface materials before extraction can begin. This process involves the removal of these obstructions to expose the underlying granite bedrock.
The extraction process starts by strategically drilling small anchor holes along the intended cutting path. These holes serve as attachment points to secure the diamond wire, chosen based on factors like granite hardness and block size. Once the wire is properly tensioned and looped around the block, diamond segments on it continuously abrade the granite, creating precise cuts with minimal waste. Water serves for cooling and lubrication during cutting. In essence, wire cutting provides a precise and efficient method for extracting granite blocks from quarries, minimizing environmental impact while maximizing productivity.
READ | Natural Stone Block Reinforcement Through Block Vacuuming Technique
Extraction of Granite Blocks
Once the granite has been cut into manageable pieces, such as blocks, heavy machinery such as front-end loaders, excavators, or heavy-duty cranes is utilized to extract the blocks from the quarry floor. Depending on the size and weight of the blocks, specialized lifting equipment may be necessary to hoist them onto trucks for transport.
Before being sent for further processing, each granite block undergoes a thorough inspection to assess its quality and suitability for use. Experienced quarry workers examine the blocks for defects, fractures, or other irregularities that may affect their structural integrity or appearance. Then extracted granite blocks are transported from the quarry site to processing facilities or distribution centres using one or various suitable modes of transport.
READ | Granite Quarries in India: A State-wise Exploration of Mines and Production
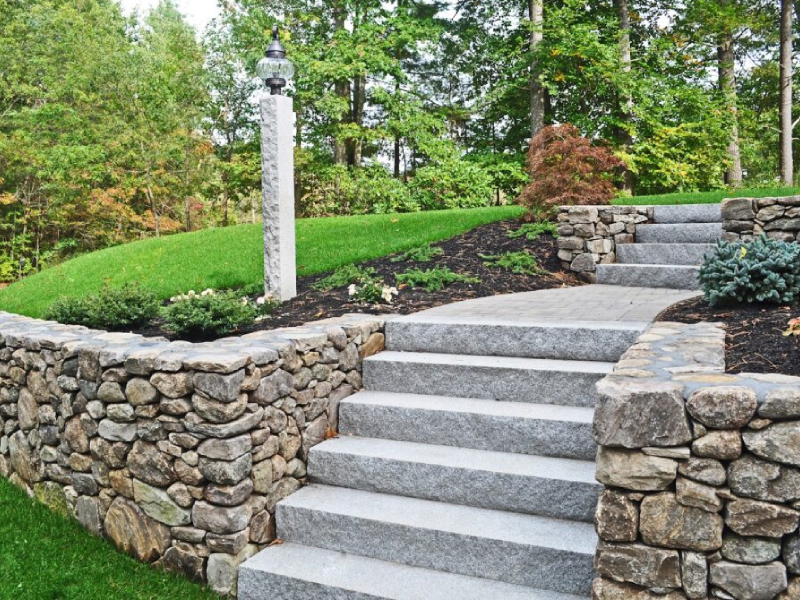
Understanding the Size, Weight, and Unique Characteristics of Granite Blocks
Granite blocks suitable for slab production come in a variety of sizes and weights, depending on factors such as the quarry’s geological characteristics and the specific requirements of the production facility. However, there are some general size, weight, and quality characteristics that are typically sought after for slab production:
Size of Granite Block
Granite blocks used for slab production are typically large to maximize the yield of usable slabs. Common dimensions for granite blocks range from several feet in length, width, and height. The exact size may vary depending on the equipment and cutting techniques used by the processing facility.
Granite Block Weight:
Granite blocks can be extremely heavy due to the dense nature of the stone. Depending on their size and density, granite blocks suitable for slab production can weigh several tons. The weight of each block is an important consideration for transportation, handling, and processing.
Quality Characteristics:
Granite blocks intended for slab production must meet certain quality standards to ensure the resulting slabs are of high quality. Some key quality characteristics include:
-
- Uniformity: Blocks should have consistent colour, pattern, and texture throughout to produce uniform slabs.
- Structural Integrity: Blocks should be free from cracks, fractures, or other defects that could compromise the strength and durability of the slabs.
- Surface Finish: Blocks should have a relatively smooth and flat surface to facilitate cutting and processing into slabs.
- Density: Blocks should have a uniform granite density to ensure uniformity in slab thickness and appearance.
READ | Where Is Granite Found? Indian Perspective In The Global Market
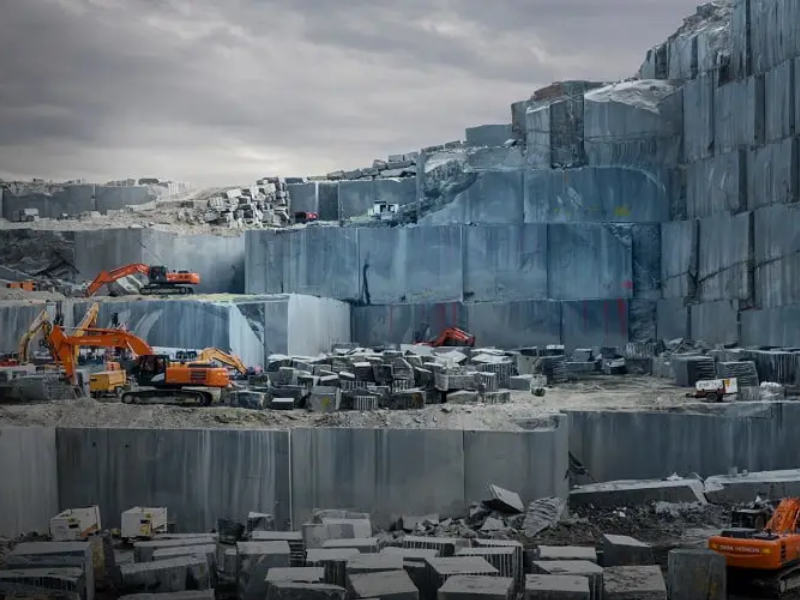
How Are Granite Slabs Made From Granite Blocks?
Slabs are made from huge granite blocks through a precise cutting process using specialized equipment. Here’s an overview of how it’s done:
- Preparation: The large granite block is securely positioned on a cutting bed or platform.
- Cutting Method Selection: Depending on the size of the block and desired slab thickness, one of the following cutting methods is chosen:
- Diamond Wire Saw Cutting: A wire embedded with industrial-grade diamonds is guided along predetermined cutting paths to slice through the granite.
- Gang Saw Cutting: Multiple parallel blades move back and forth across the surface of the block, slicing through it simultaneously.
- Diamond Circular Blade Cutting: Rotating circular blades slice through the block as they make contact with its surface.
- Cutting Process: The chosen cutting method is employed to slice the granite block into individual slabs. Water and abrasive slurry are often used during cutting to facilitate the process and dissipate heat.
- Quality Inspection: Each slab is carefully inspected for accuracy, quality, and any defects that may affect its usability or appearance.
- Further Processing: After cutting, the slabs may undergo additional processing steps such as grinding, granite resining, polishing, and finishing to achieve the desired surface texture and appearance.
READ: Granite Stone | The Journey from Quarry to Kitchen
Granite quarries extract blocks of varying sizes, recognizing that each cutting technique requires specific block dimensions. This ensures seamless integration with processing units utilizing different types of machinery, such as diamond wire saws, gang saws, or diamond circular blades, optimizing efficiency and productivity throughout the production chain.
- Extraction: Granite blocks are extracted from quarries using methods such as diamond wire saw cutting or drilling and blasting.
Transportation: Once extracted, the blocks are transported to processing facilities using heavy machinery and specialized equipment. - Cutting: At the processing facility, the blocks are cut into slabs using various cutting techniques such as diamond wire saw cutting, gang saw cutting, or diamond circular blade cutting.
- Grinding and Polishing: After cutting, the slabs undergo grinding and polishing to achieve a smooth and shiny surface finish. This process enhances the natural beauty of the granite and ensures uniformity in appearance.
- Quality Inspection: Each slab is carefully inspected for defects, imperfections, and dimensional accuracy to meet quality standards.
- Packaging and Distribution: Once inspected and approved, the slabs are packaged and prepared for distribution to customers, construction sites, or fabrication shops.
- Installation: Finally, the granite slabs are installed in their intended application, whether it be for countertops, flooring, wall cladding, or other architectural and design purposes.
By following these steps with precision and care, granite blocks are transformed into high-quality slabs ready for use in various construction and design projects.